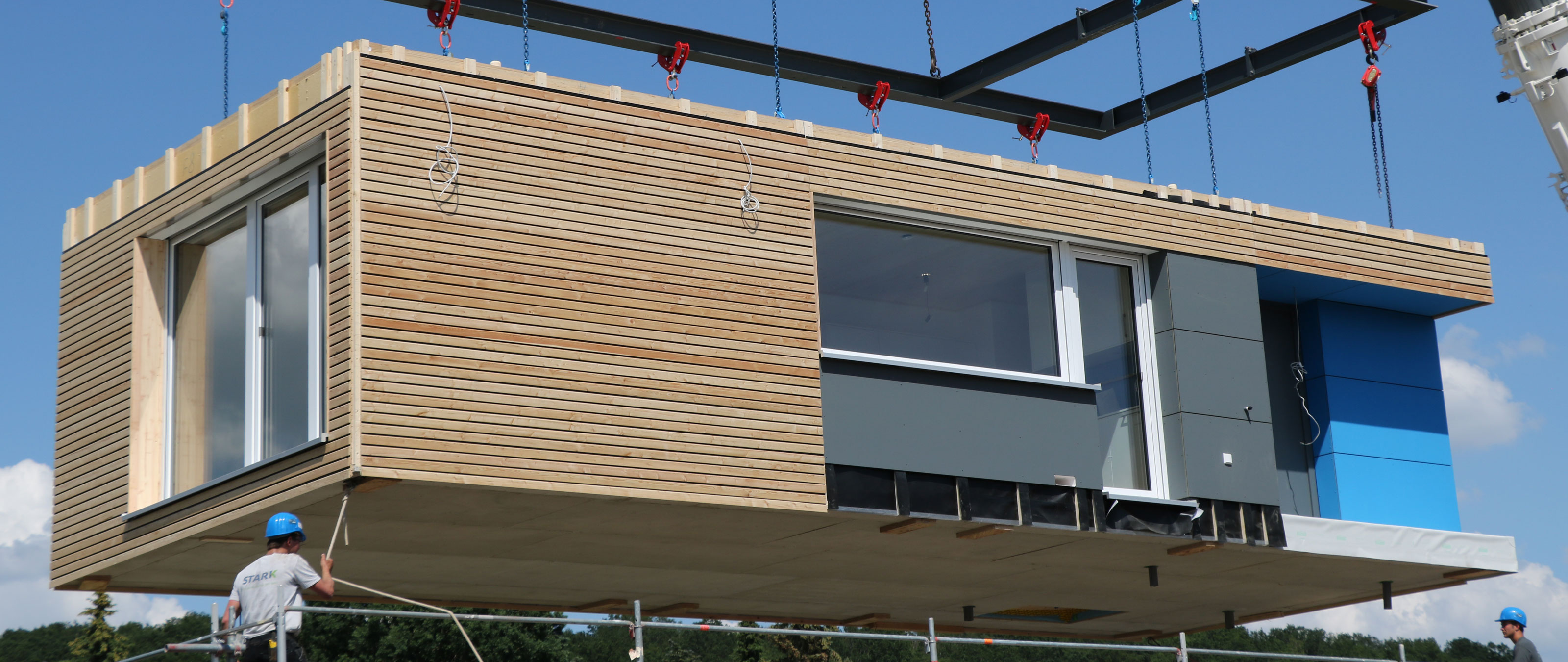
Just under ten years after it took its first steps in module construction, Zimmerei Stark GmbH in Auhausen, Bavaria has become one of the leading names in the field. This leading position is reflected in, amongst other things, the fact that the company has just secured an order for accommodation from the German armed forces. The company has 170 employees and is active in a number of sectors alongside module construction, including the construction of detached houses and apartment buildings, house renovation, the construction of halls, commercial objects, agricultural buildings and shepherd's huts. Timber frame construction still plays an important role in the company's activities as Managing Director Martin Stark believes that it has decisive advantages, particularly for individual planning and large-scale rooms. Stark GmbH has managed to develop such a strong reputation in the module construction industry by creating its own module concept. With this concept, up to five modules can be placed on top of one another without causing subsidence in the building. This is remarkable because it means that with the exception of the ceiling, the modules can be constructed from timber frame elements. "This allows us to benefit from a synergy effect because we can work with a self-contained system in both timber frame and module construction without having to switch between different details," explains Martin Stark. Wood frame elements and modules are produced to "Efficiency House" quality standard 55 or higher.
Module construction for private developers
Another factor that is responsible for the company's good market position in the module construction sector is a business model that targets not only the commercial and public sector, but also private customers. At its Auhausen premises, the company builds not only large projects such as hotels and temporary school and office buildings out of modules, but also accessible living concepts for senior citizens, "tiny houses" as a cheap initial step to owning property (over the years, these properties can be adapted to changing user demands) and mobile houses for families that, for career reasons, have to change where they live. In this case, they move — together with the house and everything in it — to a new site. Even the strip foundations laid by Stark are recyclable. The company has now patented the "living on rented ground" concept: sites in real estate hotspots that are not currently in use are rented for a specific time period and houses are built on them, enabling cheap residential accommodation in a good location. Zimmerei Stark itself runs a model module house on rented ground at Lake Starnberg. When the rental period expires, the model houses, together with everything in them, simply move to another location — no stress involved. Another special feature of the carpentry company from Auhausen is the wide range of products it manufactures: Customers can buy not only the module building but also a large proportion of the interior fixtures and fittings. The company's in-house carpentry workshop produces furniture and kitchens that can be sold — together with kitchens from other brands, electrical equipment and accessories — in the company's own furniture studio. Anyone who values convenience or who has little time can have a module house, including a bathroom, furniture and accessories delivered to their plot. A house including a kitchen is now practically standard for the company in Auhausen. "We only need to add glasses and crockery later. As a rural medium-sized company that has to fulfill a variety of different wishes, the range of service that we provide is something that distinguishes us from the big companies in the industry." In recent years, all of these good ideas have given Zimmerei Stark a stable demand for module buildings. The private house construction sector makes up 30 percent of the company's total sales — the market share for modules in this sector is 10 percent. The company began constructing modular multistory apartment buildings for the public and commercial construction sector in 2018, and has achieved a market share of 5 percent. Over the last nine years, the company has produced and assembled 130 modules. The company also anticipates strong growth in this business area in the future.
Extensive restructuring
This development is reflected not only in a state-of-the-art, model module house at the company's site, but also in a company structure that has been adapted to the new objectives. The company recently began operations from a new hall that allowed the business to take the step from manual to automated production. The right-hand bay of the production hall houses the new production line for timber frame elements, at the heart of which is a WEINMANN WALLTEQ M-380 insuFill multifunction bridge with an integrated blowing plate and two work tables. The blowing plate has a control system that enables material to be blown into even very small cavities fully automatically. A third WEINMANN assembly table for assembling facades and a work table for special elements complete the production line. A distribution trolley transports finished elements on to facade construction, window installation, interim storage, the loading station and the module station. Here, a crane picks up the timber frame elements and transports them to the 100 m long module rail system in the left-hand bay of the hall. It is here that the modules are assembled. Using this system, Stark employees can manually push modules weighing up to 25 t along the rails to the individual workstations. To separate the processing activities from the assembly work, the post and panel processing work is performed in a separate production hall. In Auhausen, the WALLTEQ M-380 insuFill is used to secure sheathing and to blow in insulation.
Specifications with a number of requirements
Planning and equipping the hall was the result of a preparation process that lasted three years. "We gave ourselves a lot of time to compare different systems and manufacturers and check them based on our specifications." The production line from WEINMANN fulfilled by far the most requirements, which included the combination of element processing and fully automatic insulating, as well as the ability to produce very heavy elements weighing up to 3.5 t with dimensions of up to 3.70 m x 12.00 m. The custom hall layout, the planning of the workflow, the proven distribution trolley and the proximity to the manufacturer were all arguments in favor of the machine manufacturer from St. Johann-Lonsingen: "Added to this was the skillful support of our project manager, later supplemented by the excellent collaboration with the machine engineers. Looking back, I can say with 100 percent certainty that we made the right decision — particularly when I hear stories from other timber construction companies about what works or doesn't work in their production process," concludes Martin Stark. He rates the startup phase of the new production technology at his company as "very good. We started production from a standing position."
Extensive digitalization
To achieve this goal, the company prepared meticulously for the new technology. Almost two years in advance, the company engaged an engineering consultant to optimize workflows and details to match the new machines. "When the technology was arrived at the production hall, we already had the digitalized details on the computers." But it wasn't just the details: The company also created macros for every type of wall, door and window. These macros now just have to be incorporated into the relevant files during planning. This step means that a large amount of element planning is already completed. By putting in the extra effort in advance, the company is able to save time and costs today. And the company has gone one step further: "To integrate the whole process, from factory planning, through work preparation right up to production, we installed the granIT software as the higher-level process control system. It allows us, for example, to also produce multiwalls. This means that we can optimize our workflow and our trailer utilization." The loading process is already largely digitally controlled: Data about the volume and weight of components is already available from the work preparation stage. Employees in other departments of the company now also work almost exclusively on the computer. Every project in the company follows the digital workflow and its status is updated continuously: from the digitalization of the construction site, measurement with a tachymeter, planning, statics, work preparation and CNC production right through to assembly. Processes such as costing, purchasing and final costing are processed largely automatically based on the data collected. For Martin Stark, the result is a "continuous process in which we will continue to develop and improve."
Higher quality at the workstations
At first glance, the extensive list of steps the company has taken in recent years may seem overwhelming. This was the case for some employees when the extensive digitalization of all processes was discussed before beginning the project. "What people were most afraid of was not being able to keep up with this type of rapid development," remembers Martin Stark. And today? "The skepticism of four years ago has evaporated, the employees are happy with their comfortable, ergonomic workstations in bright halls with underfloor heating. Many of our trainees remain with the company. Everyone pulls together, everyone makes progress and gives their all." Some employees have even been able to keep their job because of the restructuring — for example, module construction has meant that some employees have been able to transition to painting facades in the hall once they are no longer allowed to climb up onto the frame for health reasons. The promise to keep on all employees who committed to the company until their retirement was one of the reasons why Martin Stark wanted to start module construction: "It allows us to create jobs for older employees with limited physical ability who we would otherwise not have been able to retain." Of course, the businessman also sees other advantages to module construction: "Synergy effects and cost benefits thanks to repetition, a high level of prefabrication, high-quality production regardless of the weather, short assembly times, particularly with a long delivery time." In conclusion, Martin Stark explains his understanding of "short" using the example of a semi-detached house with four modules that has just been constructed: "The modules were delivered for assembly on Sunday night and were assembled by 11:46 on Monday. Our employees were then able to remove the truck-mounted crane and go home."
Photos: Dr. Joachim Mohr
“This allows us to benefit from a synergy effect, because in timber frame and modular construction we work with a self-contained system without switching between different details.”Martin Stark, managing director Zimmerei Stark
Zimmerei Stark GmbH
Founded in 1920, the Zimmerei Stark now employs over 170 people and is one of the largest suppliers in this region. At the Stark company, tradition is combined with state-of-the-art technology.
Website