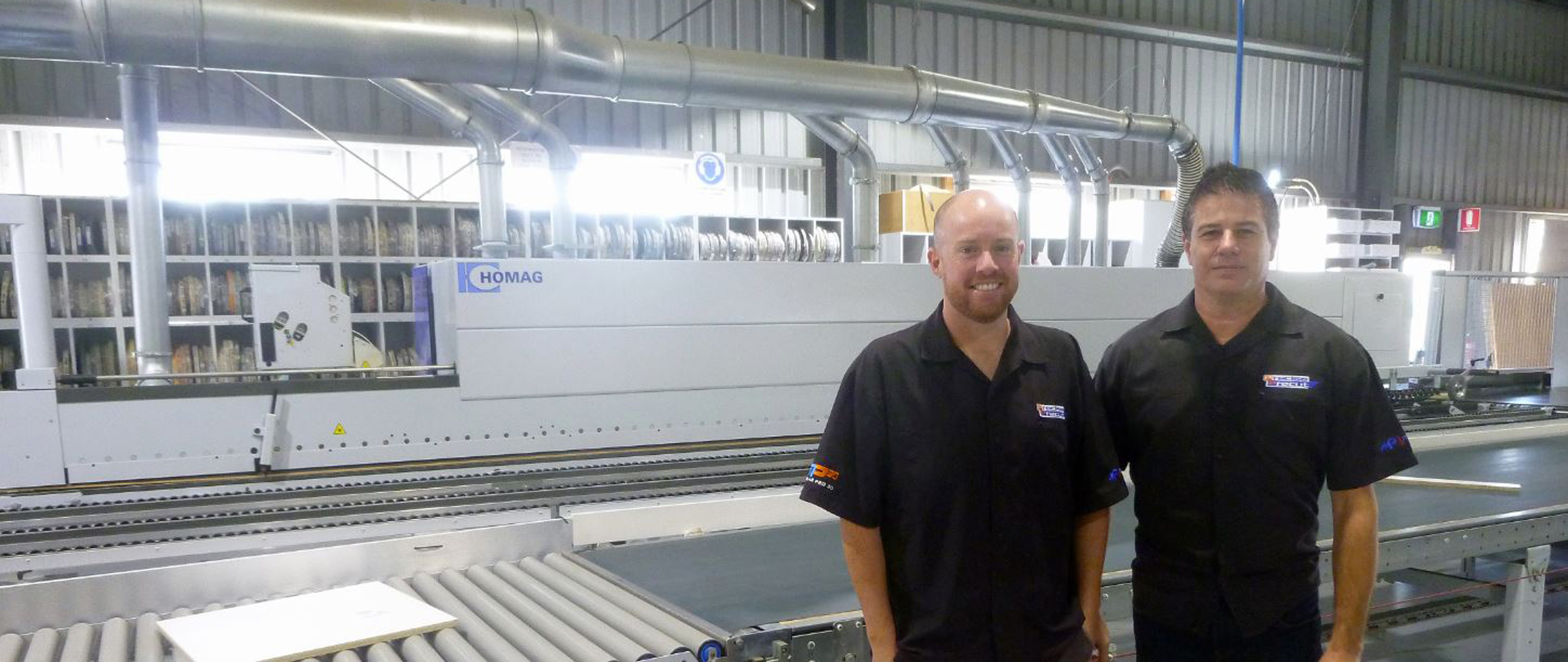
An article which was published in the AWISA Magazine, Summer edition 2016.
<link http: www.awisa.com _blank external-link-new-window>www.awisa.com
Today’s quality expectations imposed on woodworking shop production are just as high as for industrial manufacturers. Therefore, Brandt and Homag offer zero joint technology for woodworking shops. Both technologies are used by companies around the world that want the best possible result they can buy. In case of hot air technology the function layer on the edge is reactivated by means of compressed hot air, creating a jointless result.
The airTec systems were developed to meet the needs of woodworking shops that look for a lower level of investment than laserTec which Homag invented, while offering the similar high standard of quality as laserTec but designed for shorter runs. The first Homag airTec machine that had been installed in Australia is at Precise Precut on the Gold Coast in Queensland. Precise Precut is a cut-to-size company that has become well-known in the region for its reliable quality service.
New business opportunities thanks to airTec
In order to offer an even better quality product at a more competitive price, director Aaron Phillips and manager Lyle Kearns decided to invest in a highly innovative technology. Aaron and Lyle saw the zero joint technology for the first time at Awisa 2012; two years later they experienced airTec live at the Homag booth at Awisa. In the following year, they purchased the Homag KAL airTec edgebander. “We had no concerns with the technology as it was already sold in Europe”, Aaron says. “We were pretty confident with the investment.”
Precise Precut use the airTec machine for the processing of their fusion doors and for carcasses. Aaron not only appreciates the superb edge quality they achieve on the machine but also the consistency. “We run multiple shifts and only need two people per shift. If we run the machine to full capacity, we may need to allow 3-4 staff to be able to keep with the machine. It’s that fast.”
For even more efficiency, they decided to invest in a Boomerang return system from Homag Automation. In a two-shift-operation, Precise Precut manufacturers approximately 16 kitchens a day. Thanks to the seamless edge produced through airTec, Precise is heading more and more into the door market, especially with the processing of fusion doors. “We are now able to target those big cabinetmakers we couldn’t previously”, Lyle says.
“Homag ticked all our boxes”
Aaron summarises the decision to team up with Homag, “The Homag KAL edgebander ticked all our boxes with no compromise high end specification and is the fastest hot air machine on the market. We also process a lot of EVA and allows the quickest change over at a flick of a switch, and, last but not least, you deal directly with the manufacturer. Before a problem escalates, Homag in Germany has an answer already. We are very happy with the support we get from them. I can already say we have increased our productivity and therefore, our margin. Without the machine we wouldn’t be where we are now.”
Innovative cut-to-size service of excellent quality
Precise Precut is a production-orientated business and they have sold cut-to-size flat packs to the trade from the very start. Aaron could see an opportunity on the Gold Coast to open a precut business as there was only one other company doing precut at a high level and knew that some competition was needed. Shane, the owner of Gold Coast Post Forming and Aaron’s father, also agreed with Aaron and partnered with his son in the business. They began business in June 2006 with two staff members in a modest 270 square metres factory behind Gold Coast Post Forming at Arundel on the Gold Coast.
Since then Precise Precut has moved forward in leaps and bounds. Accommodating a 1,300 square metres factory, the Queensland company has grown to employ 25 staff.
Online ordering system for better customer experience
The next evolution in Precise Precut was its in-house online ordering system called Modular Pro that Aaron and Lyle are very proud of. “The program lets our customers order their cabinets online without having to do a lengthy cut list”, Lyle explains. “We now have 95 per cent of our customers using the online ordering program.” Currently, Precise is working on a new programme that features 3D capabilities. “We do it a bit differently than others and look and think outside the square”, Lyle says. “We get our ideas from customer requests and ask ourselves if there’s an opportunity for a commercial development.”
Due to the fact that the whole cutting process is automated these days, Aaron and Lyle are now looking into a storage system from Homag Automation. “We have had a taste for what these machines can do for our business; hence we are going to automate as much of the process that we can. This will streamline our business even more. Bringing down our delivery times and making an even more affordable cabinet,” Aaron says with a smile. “Watch this space.”
Why airTec
- No visible glue line
- Simple operating process
- No waiting times and setup costs for glue colour change
- No contamination and cleaning problems
- Significantly higher adherence force of the edge compared to hot melt glues
“The Homag KAL edgebander ticked all our boxes with no compromise high end specification and is the fastest hot air machine on the market”Aaron Phillips, Director, Precise Precut