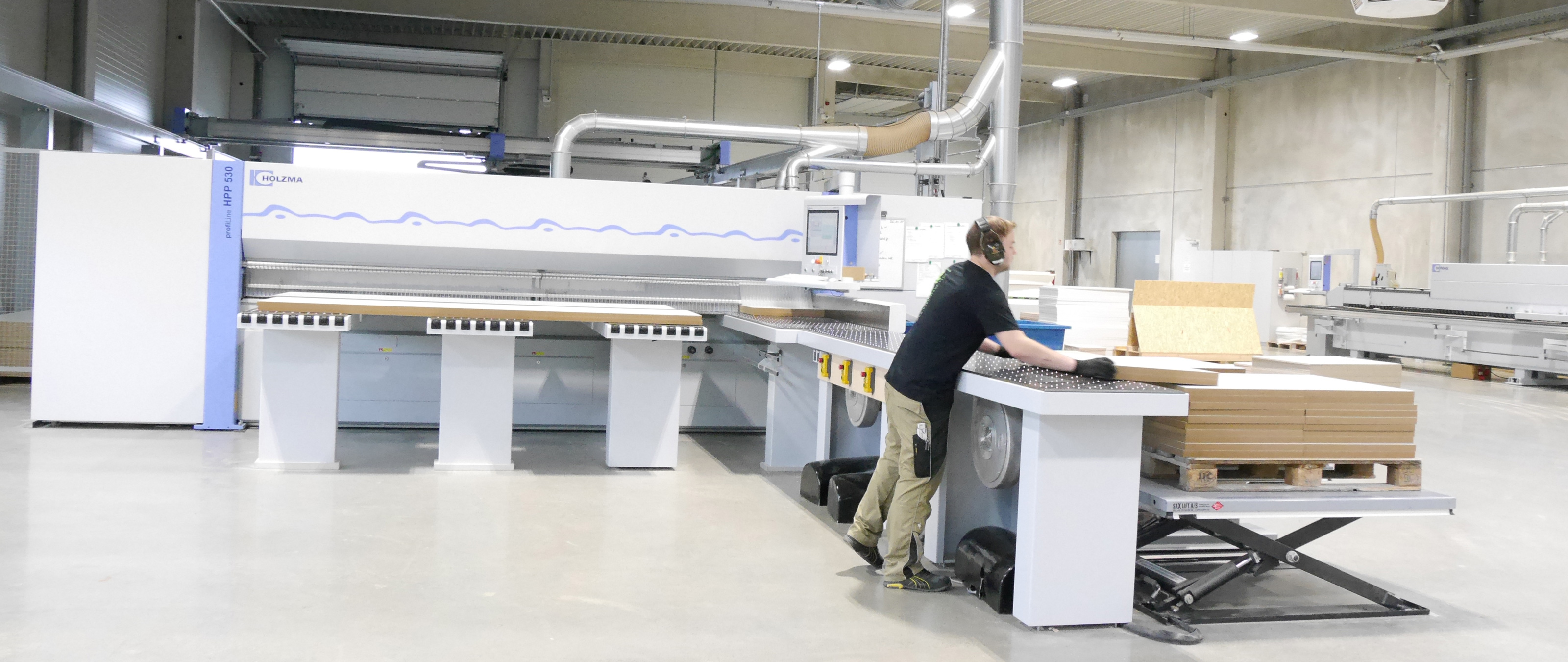
An article from the specialist magazine DDS, 01/2016, <link http: www.dds-online.de technik maschinen-werkzeuge hier-bueckt-sich-keiner-mehr external-link-new-window>www.dds-online.de
"No more bending over"
No matter what needs to be cut – one or one hundred of the same decor panels, hard foam panels or just two HPL sheets – at Popp, one single person can handle it with a saw-storage cell from Holzma and Homag Automation. No bending over – and no need to carry anything either.
Clemens Simon at Popp in Forchheim handles two panels at once on the saw with ease on his own, MDF 22 mm thick, 4100 x 2800 mm. For the larger series, he even cuts packages up to 115 mm thick comprising five or six panels. The program allows the "HPP 530 ProfiLine" from Holzma to initially cut the package into four or five strips that are 4100 mm long and perhaps 300 to 500 mm wide. The Popp joinery supplies series and one-off products to industrial companies, but also to universities, councils, retirement homes and private customers. Its strengths include series products made from timber materials and high-tech materials for medical technology devices. Popp is also a 3D milling specialist. Frank and Sonja Geppert now lead the company founded by his great grandfather in 1905, and the master joiner has developed the business into an industrial supplier. The company employs 60 staff, moved to a new 6000 m² building two years ago and produces at a very high level of technology. In addition to the timber workshop, it also offers plastics manufacturing.
Pushing instead of lifting
With three or four strikes against the edge of the waste container, Clemens Simon shreds and disposes of the trimmed offcuts. Then he pulls the strip packages right to the front on the table extensions mounted perpendicular to the sawing line. This does not seem to be particularly difficult for him. That is because the machine table and the table extensions have a grid of air nozzles. Where the panel package presses a ball down, air flows out and virtually lets it float. Whilst Clemens Simon is cutting at the front, the "TLF 411" automatic panel storage unit from Homag Automation is working in the background and carries the material for the next package to the rear part of the saw, the feed-stacking table. When the last strip is cut and the rear offcut disposed of, Clemens Simon turns and pushes one strip after the other against the right-angled fence and into the right-hand gripper of the material pusher. Controlled by the program, the saw now divides the strips according to the length. With each cycle, a package of finished cuts is pushed onto the front table. Clemens Simon has to sort them for subsequent processing and distribute them onto three stacks. This work clearly does not seem difficult to him either. The air cushion table in front of the right-angled fence is extended forwards by approximately 4 m. Behind this are lifting tables for the individual stacks. The top panel is automatically always a few millimeters below the table level. Without having to lift anything, Clemens Simon can push panel packages onto their respective stacks quite easily. Now the cell interrupts the series operation and pushes a special production in between. A sandwich made of a very high-quality hard foam core and HPL covers for a medical device is to be produced. The storage unit and the saw handle these materials with no problems as well.
"All objectives achieved"
Before the joinery moved to Forchheim from neighboring Baiersdorf at the end of 2013, the employees were only able to handle cutting on a similarly sized Holzma saw with hard manual work. Then, like today, the panel quota to be divided was delivered just in time; approximately 30 panels daily. The Gepperts wanted to use the move to ensure that their employees would no longer have to lift the panels, so they invested in the cutting cell. In addition to the saw-storage cell, the hall boasts four processing centers, an edge banding machine and a dowel machine, all from the Homag Group. The investment has been worth it for Frank Geppert: "We have achieved all our investment objectives: No bending over, no laboring and no searching any more either. What previously took two men eight hours to cut can now be completed by one in just seven hours. The cell also handles all of our materials. Offcuts don't give us any problems, as we can cut all panels completely as a series manufacturer."
Images: specialist magazine DDS / Georg Molinski
“We have achieved all our investment objectives: No bending over, no laboring and no searching any more either. What previously took two men eight hours to cut can now be completed by one in just seven hours. The cell also handles all of our materials. Offcuts don't give us any problems, as we can cut all panels completely as a series manufacturer.”Frank Geppert, Managing Director Popp GmbH & Co. KG