You are interested in
Discover our knowledge and solutions for Door Production
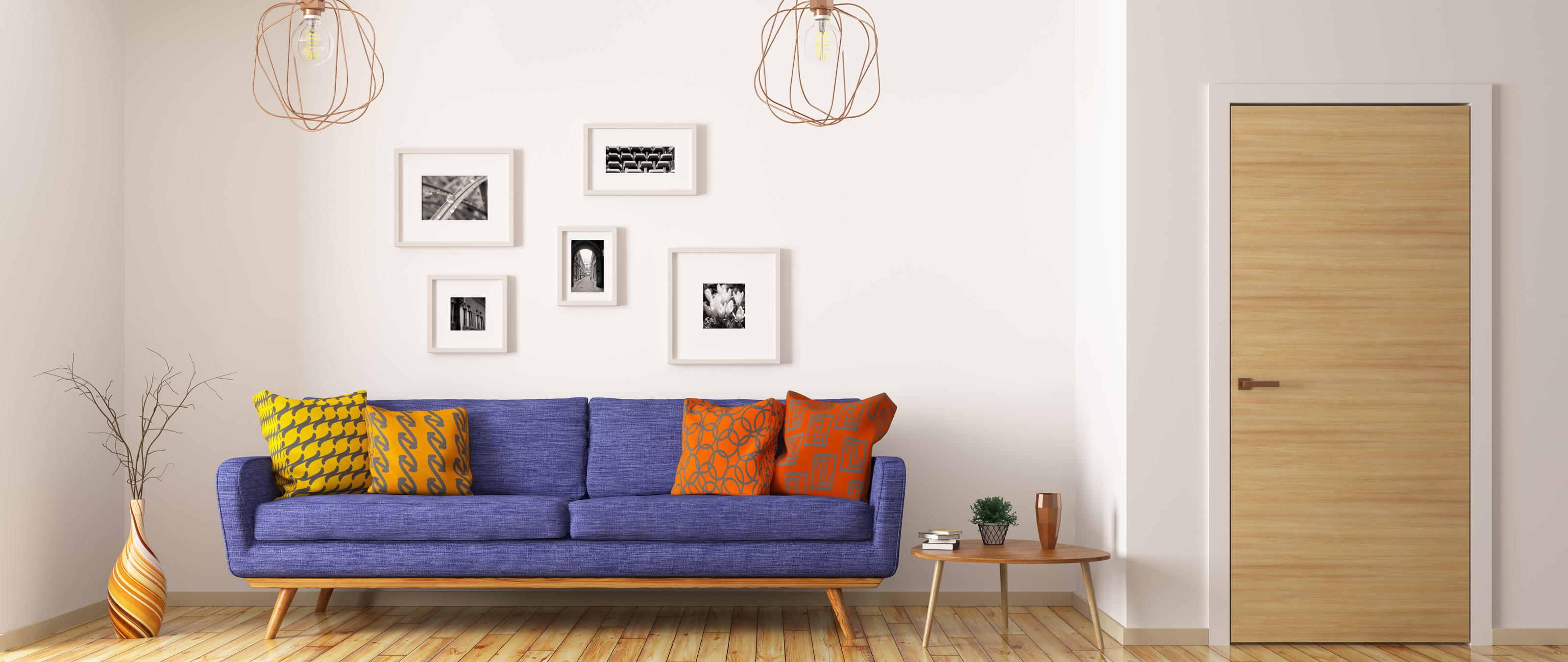
We offer individual machines and fully interlinked systems for every process step, from cutting the raw materials to size, right through to packaging.
From 3 to 3000 doors per shift. From fire doors and soundproof doors to normal interior doors. Whether the paneled doors are solid, veneered or film-coated, or the door leaf consists of three, five or more fillings. The range of options and geometries is almost unlimited.
Industrial plant technology
We provide extremely cost-effective, high-performance plants and systems for producing door elements, from creating the blank right through to packaging and the fully networked system.
Door leaf production
Use our machines to produce anything from 30 to well over 1000 doors per shift. The degree of automation depends on the batch sizes you require. A central control system prepares the data and tracks the parts during production.
No matter what kind of door leaves, and no matter the quantity you would like to produce, we will work together to find the right solution to meet your needs.
Fully networked — from cutting through to packaging
- Performance and functions of our machines:
- Cutting raw materials to size
- Preparing veneer
- Producing door leaf blanks
(producing middle layers, assembling, cutting, positioning, gluing, pressing) - Format/edge processing
- Sanding/painting
- Lock/hinge processing
- Trimming/cut-outs
- Automated handling at all processing stations
- Packaging
Door Frame Manufacturing
Whether you want to produce surrounding frames or block frames, we can develop the right solution tailored to your requirements. Our machines are suitable for small and large batch sizes, from gluing the individual frame parts, to the complete packaged frame, with an output of 30 to more than 1000 frames per shift. Equipped with state-of-the-art control technology and a level of automation to suit your production volumes.
- Loading
- Cutting raw materials to size
- Production of risers
(profiling, coating/wrapping, direct post-forming) - Production of panel brackets
(banding moldings, profiling, coating/wrapping of brackets) - Wrapping block frames
- End, hinge and striker plate processing including assembly
- Packaging
- Stacking/palletizing
Door processing with CNC technology
Stationary technology provides special solutions for particular applications, such as rabbet gluing for veneer edges. In addition, stationary technology offers formatting and profiling, through to window cut-outs and fixture processing, and finally surface processing using tracing units.
CNC technology: The perfect entry-level solution
- Suitable for processing door panels and frames
- Possibility of multi-location and alternating operation
- Free configuration of tools and units ensures high flexibility
- Wide variety of tool changers, table designs and clamping equipment
- Manual infeed of door panels, e.g. using vacuum suction device
CNC technology: A solution for special applications
- Flexible door leaf processing
- Use in interlinked lines or with automatic handling
- Compact construction
- Option of integrated workpiece cleaning
- Automated operation, e.g. using barcode identification
- Option of flexible panel size processing with regard to dimensions and profiles
- Plus window cut-out processing
CNC technology: Fully automated high-end solutions
- Up to four trimming spindles with HSC technology and 28 kW, plus five-axis processing
- Fully automatic positioning of suction device, suitable for a wide range of workpiece geometries
- Automated handling (unmanned production)
- Integrated workpiece cleaning unit
- No danger of collision with the machine during handling thanks to separate infeed and processing areas
- Six-sided processing possible thanks to integrated turner
- Automatic program generation and connection to ERP and/or production control systems
Videos
Project planning by HOMAG
We develop suitable solutions for your door production. Right up to a fully networked system. From design to delivery. From the first meeting to completion of the project.
Mehr Informationen