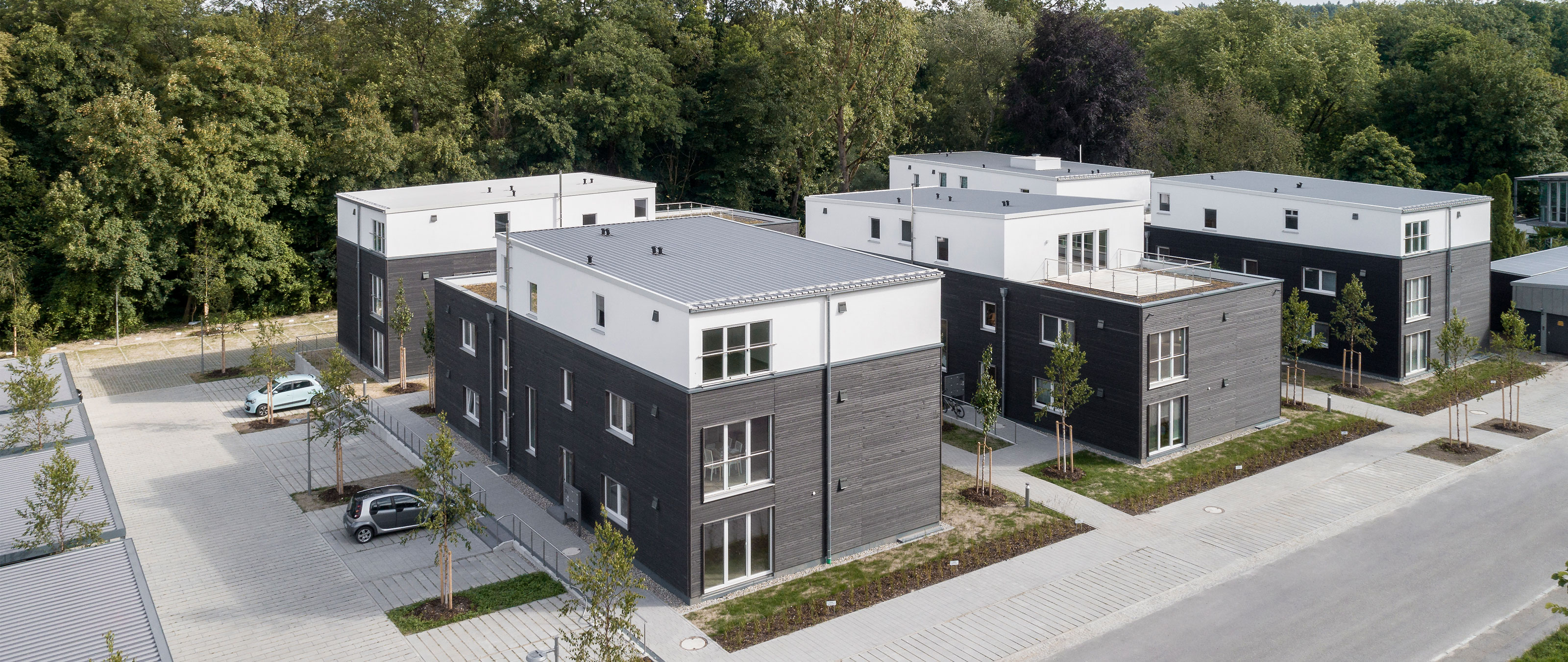
The fact that the company has been involved in apartment construction for many years is currently proving to be very advantageous. In 2022, there were a number of shifts in timber construction in Germany. The discontinuation of a special funding program in Germany led to a slump in the construction of detached houses, and higher interest rates, energy and material costs—along with general political uncertainty—exacerbated this negative trend. The market has since recovered slightly, but in the detached house sector, the signs indicate a decline for the time being. Many timber construction companies are therefore searching for new business areas, such as apartment construction, without leaving the detached house construction sector behind completely.
Involved in apartment construction since the 2000s
Haas Fertigbau GmbH, based in Falkenberg, Bavaria, started constructing apartments in the 2000s, so when the slump in the detached house market occurred last year, the company was in a comfortable position with alternative business areas already at its disposal. The construction of detached and semi-detached houses accounts for the lion's share (60 percent) of the annual turnover of the Haas Group, which totaled EUR 250 million in 2022. The remaining 40 percent of the company's annual turnover is generated by commercial construction, which is divided into the areas of industrial and commercial construction, apartment construction and the construction of agricultural buildings. Apartment construction is currently experiencing the strongest growth of all business segments.
As far as residential buildings are concerned, according to managing director Xaver A. Haas, the company is building "what it can and what makes sense." In other words: residential buildings with up to four stories, turnkey, energy-efficient and sustainable. Apartment construction is divided into two areas, for which the sales channels in particular are different.
Under the heading "WOB small," smaller residential buildings with up to 15 residential units are processed for private investors, who have become aware of the company through targeted advertising and, in some cases, also through the detached house sector. "WOB large" refers to the construction of residential complexes with 15 to 40 residential units. Customer contact is handled by specialist media, architects and project planners.
Apartment construction to alleviate the effects of the detached house crisis
Both areas of apartment construction are on the rise and, in 2022, helped to partially compensate for the slump in detached house construction — which amounted to 30 percent for Haas. This development did not hit the prefabricated timber house company as hard as some competitors for other reasons too. For example, only half of the total 700 prefabricated houses are built in Germany; the rest are produced in Großwilfersdorf, Austria, with some being sold in Austria, and some to the Czech Republic via a sales office in Prague. The decline in detached house construction was much less severe in both of these countries compared to Germany. Nevertheless, the company must still ensure that incoming orders don't stall completely in Falkenberg. The high quality of products helps the company in this respect, with target groups that are interested in topics such as energy efficiency, sustainability, ecology and smart home technology. Against this background, QNG certification is not a problem either, meaning public funding can be offered to those interested in construction through interest rebates, which is quite attractive given the current interest rates. This also helps in the field of apartment construction, which the company did not neglect when the detached house market reached its peak. "In recent years, we could have profitably focused on detached house construction, because the effort and cost pressure for this sector were low and the margins were very high," explains Xaver A. Haas. Nevertheless, the company retained its diversified nature even during this period.
Flexibility instead of maximum efficiency
This is particularly evident in the area of production, in which the company invested in three stages under the pressure of increasing demand: In 2018, wall element production was automated at the Falkenberg site, a similar production line followed in Großwilfersdorf in the summer of 2022, and in autumn 2022, the company converted its hall to enable a roof and ceiling element line in Falkenberg.
At the top of the specification for WEINMANN—which designed and delivered all three production systems—was the demand for flexibility, which also included possible options for future process steps. In any case, the management team wanted the production plant to reflect all areas of the company — including all disciplines in house and commercial construction, including agricultural buildings.
"We looked at the production systems from several competitors," recalls Xaver A. Haas: "It became very clear that optimized lines for prefabricated house production are geared toward absolute efficiency. However, they can only produce detached houses with a high degree of standardization." With highly standardized elements, the cycle times on such systems are up to 7 minutes per element, but at Haas, the cycles are significantly slower, at 30 minutes. Current changes in the market, however, mean that this reduction in efficiency represents a great gain for future viability thanks to increased flexibility.
The flexibility of production at Haas is initially evident in the element heights: In Falkenberg, prior to automation, manual production was set to an element height of up to 3.11 m, but today, elements with heights of 1.50 m to 3.50 m can be produced. "High walls are now practically standard in residential and commercial construction, since more and more building technology has to be accommodated in the floor and in suspended ceilings," explains Xaver A. Haas. High walls are also in demand in terms of spaciousness and elegant ambiance — not only in commercial construction, but also in modern detached house construction. The height of the elements that are 1.20 to 12.00 m long is also exceptional at up to 50 cm. The same applies to the maximum weight of 3.5 t — an absolute novelty, especially if, like Xaver A. Haas, you want to clad these elements with gypsum plasterboard panels and then run them through the line without any damage: "Of course, this was a challenge, nobody had done that yet, which is why we re-optimized these details of the line for quite a while. WEINMANN was very committed to the development and, in the end, always found optimal solutions to meet our requirements."
The end result was a win for both partners. With the pilot project, WEINMANN anticipated a development in timber construction that has long been a reality today. Haas Fertigbau acquired a production line that can do everything the company needs: Exterior and interior walls for house and apartment construction, walls for commercial buildings, commercial and agricultural halls, facade systems and special components such as gables and jamb walls. Everything that is industrially feasible runs via the automated production line; the few exceptions via a manufacturing facility next to the wall slot.
Complex process steps are outsourced
The high degree of versatility and the high number of units corresponds to a high level of machine use. In Germany, the production line for wall elements consists of three rows of tables: In the first row, a WEINMANN FRAMETEQ F-700 frame work station is followed by a WALLTEQ M-380 multifunction bridge with two tables plus an encoder for the turning operation; in the second, there are three other tables and a second WALLTEQ M-380. Buffers for complex work are available in both rows. Panels are deposited by lifting equipment and the insulation is applied manually in order to be able to meet a wide range of customer requirements in this area. With the two multifunction bridges, throughput can easily be increased during peak times, for example during the production of a larger residential building, and bottlenecks are avoided. The third row of tables is used for the same purpose, to which process steps such as the installation of the external insulation are outsourced. The work is manual here too, which goes along with great variability in the facade systems. Finished elements end up on a truck lifting platform with a tilt table, which transports them four meters down into a lower part of the hall and stores them in two wall slots with a capacity of 3000 m2. This is a "show effect" staged for the customers via an observation platform, which is due to a height offset due to the slope of the hall.
The company also focused on flexibility in the upright storage systems: A total of three distribution trolleys enable flexible storage, relocation and removal from storage, which means that when execution of a large building is delayed, this does not become a bottleneck for other projects. Finishing is also executed in the storage system, with plaster application and window installation.
In Austria, due to the limited space, the company restricted itself to a somewhat smaller solution with a "pull-out table" for the faster inner walls, while roof and ceiling element production in Falkenberg was able to draw on unlimited resources after the hall conversion. The WALLTEQ M-380 used here travels over three tables, is equipped with a unit for laying and attaching roof battens, and can also lay shuttering if required. Here, too, there is a parallel row of tables as a buffer for complex process steps, such as for insulation and later perhaps for installation of power and water lines — this is not an issue at the moment, but "you never know where the journey will take you." The element width is up to 2.50 m, the standard length is 14 m and can be increased to 18 m using blocks. "14 m allows me to have two elements per table and thereby speed things up," explains Xaver A. Haas. "In addition, employees can produce two opposite mirrored roof sides at the table simultaneously with this length, which simplifies the process for them. We need 18 m if we are working with a three-field system in commercial construction."
Outlook
Finally, it should be noted that Haas simulates and optimizes all production processes digitally before they run over the actual machine twin. What's more, thanks to the use of Autodesk Revit, laser scanners and tachymeters, when it comes to commercial construction, the company is already one step ahead in the digitalization of all processes than the majority of comparable projects in Germany.
For the production plant, the company is currently considering an extension with automated plaster application, as well as a panel processing center. It is intended to alleviate a bottleneck that can arise in certain processing configurations. The company is not currently planning to get a robot: "Too optimized to cycle times and therefore too rigid and inflexible." Xaver A. Haas thinks that the weighting of the business areas will change for the future development of the company: "There will be a stronger shift toward apartment construction. We will invest less activity in detached house construction and then the quantities will even out again. In the long term, the trend continues toward apartment construction." The company's policy of keeping all options open with many business areas has therefore paid off.
“WEINMANN was very involved in the development and in the end always found solutions for our requirements that were good and fit.”Xaver A. Haas
Haas Fertighaus GmbH
Haas Fertighaus was founded in 1972 by Fritz Haas, whose goal was to build prefabricated houses of the highest quality. Today, Haas Fertighaus is one of the leading providers of custom prefabricated house planning and construction services in Germany and Europe. The company places particular importance on sustainability, using environmentally friendly construction materials and a resource-saving construction process. In addition to traditional single-family houses, Haas Fertighaus also offers apartment buildings and commercial construction solutions. With its broad range of services and high-quality products, Haas Fertighaus has established itself as a reliable partner in the field of custom house construction.
Learn more