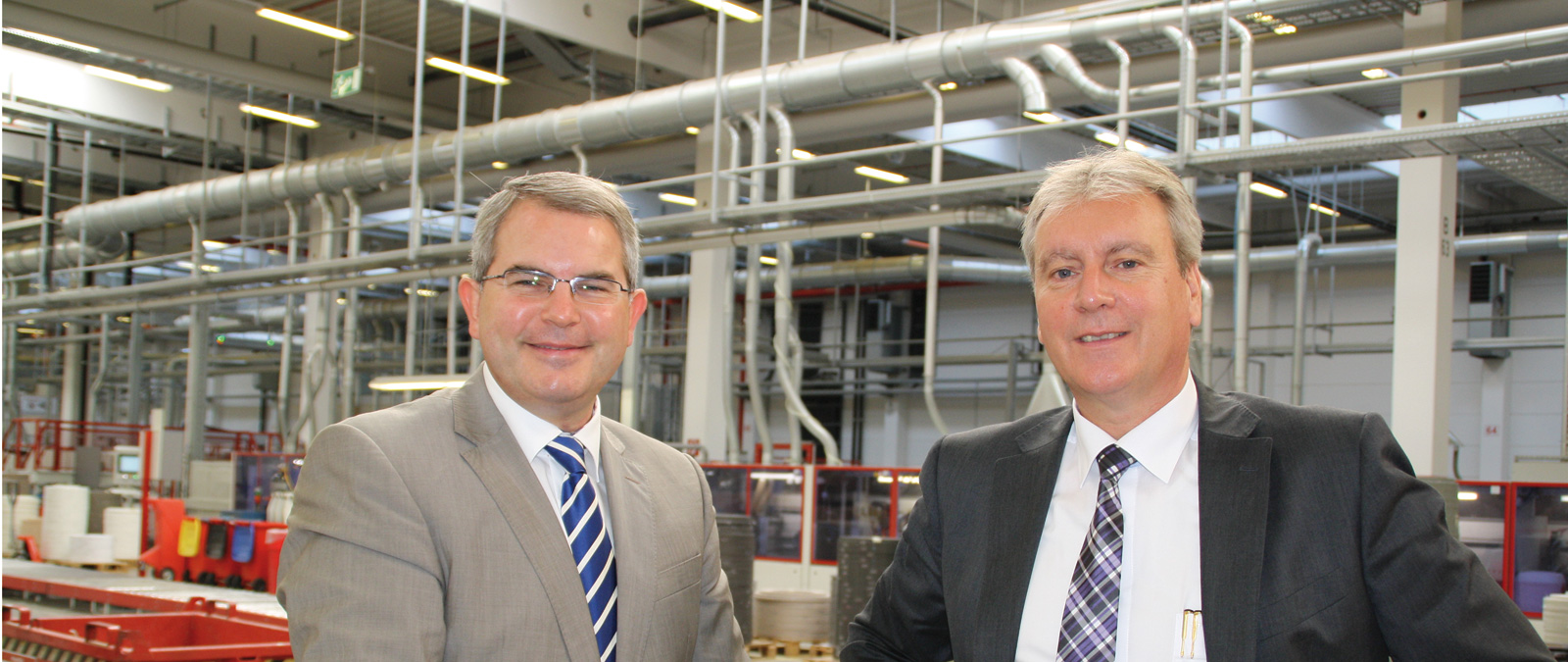
The powerTouch system offers many benefits, including the elimination of interface issues within a plant, reduction in training time for new employees, and direct generation of key performance figures for a particular machine directly from the controller.With revenues of EUR 923.4 million and 80,000 kitchens produced in 2013, Nobilia is an undisputed industry leader. However, in order to achieve equally impressive production figures, it needs a fast, flexible and efficient production system that can keep up with its annual rate of sales growth. "For Nobilia, it is hugely important to have and to maintain a high degree of machine utilization. We don't have a finished goods warehouse that we use to supply customers. Instead, we start production only once an order is received, in accordance with the delivery schedule," explains Martin Henkenjohann, Technical Director at Nobilia for the last four years and responsible for the plants at Kaunitz and Verl-Sürenheide, Germany. "Individual parts are manufactured at a very early stage in the process. We have to be able to complete the process on schedule so that the downstream logistics chain can run smoothly right through to the loading stage."
One step in this direction has been the purchase of two new and identical systems from the HOMAG Group for manufacturing customized fronts in both Nobilia plants. The systems include the new powerTouch machine controller. "Despite the batch size 1 production process, it is not a particularly big system. However, it has a high degree of internal complexity and is one of the first in this form to be delivered," explains Stefan Rose, Sales Director at HOMAG. Lars Eberlei, Production and Plant Planner at Nobilia and a specialist in edging for body and front areas, adds: "This system clearly demonstrates the strengths of powerTouch. It enables operation of a whole system with multiple machine components using a single, standardized control system. In this system, customized front parts that have previously been edged on three sides are automatically cut to the required fixed dimension and an edge is applied using either a laser or PUR glue. We actually use two different colors of PUR adhesive, and we stock 96 different edges using the magazine. Both the 96-slot magazine and the system infeed have their own powerTouch terminals which communicate with each other and control the other HOMAG and HOMAG Automation system components."
Nobilia is home to the first complex system to use the powerTouch controller from the HOMAG Group.
The machine infeed and the edge magazine each have operating terminals that communicate with each other.
Lars Eberlei is Production and Plant Planner and, together with six other colleagues, manages industrialization of the kitchen specialist's production facilities. Their aim is to achieve the highest possible degree of automation at maximum machine efficiency. ...
Published in möbelfertigung /2014. Many thanks to Doris Bauer.