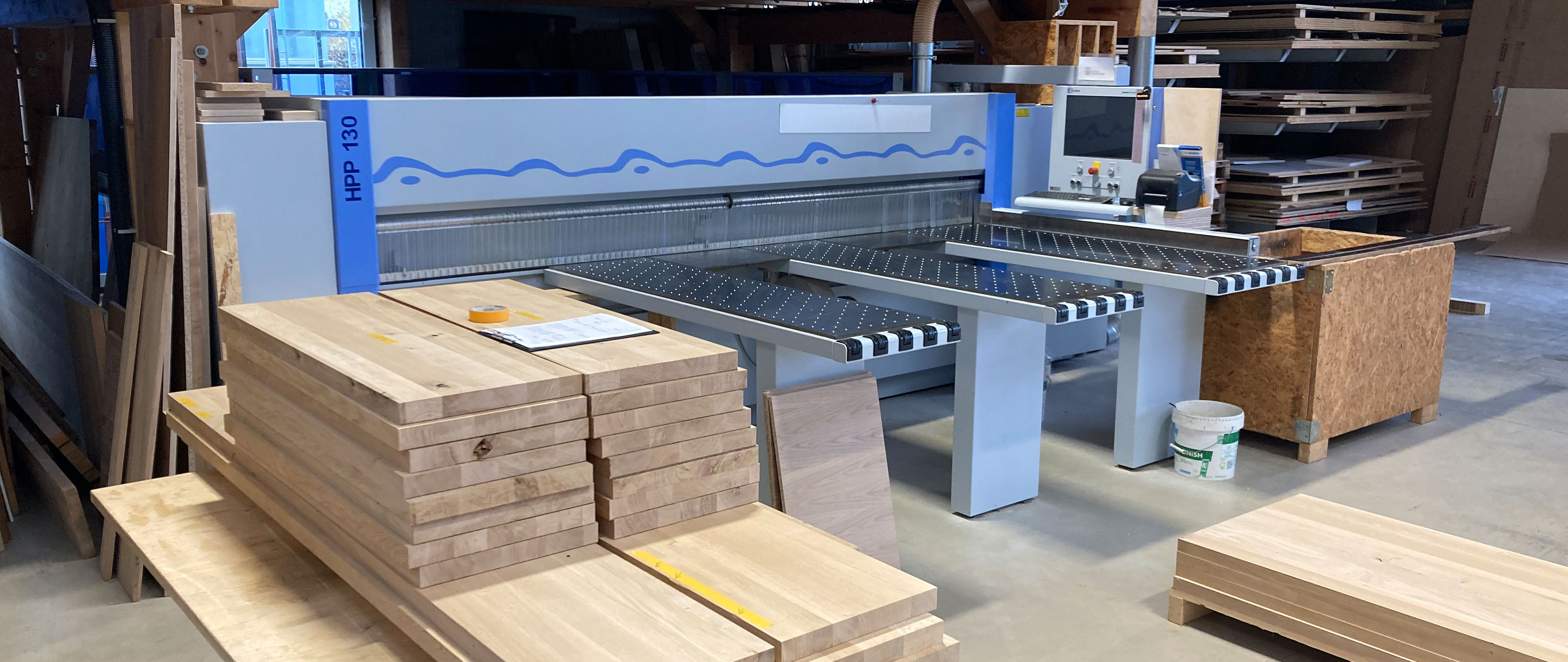
Stephan Ganz's business, which employs 10 people, is based in Rimpar, Germany, near Würzburg. Over an area of 960 m², of which 60 m² is allocated to office space, he creates many custom items for his customers, who are all within a radius of 100 km. Whether it's kitchens, staircases, doors, bathroom furniture, floors or even complete interior fittings, everything that can be produced from solid wood or wood panel material is in excellent hands at the Ganz joinery. There, they know how to reinterpret classic elements such as solid wood and combine them with panel materials. They specialize in producing completely custom batch size 1 concepts for their customers.
"In relative terms, 25% of our orders come from tradespeople and 75% come from private clients," he confirms. Stephan Ganz also prefers to cater for private customers, as the individuality of the services and requirements is greater here and the orders are therefore more attractive and interesting for him.
Focus on training
Stephan Ganz is very keen on promoting young talent and this is very important to him. Two young carpenters are always trained every apprenticeship year. In a similar way to his own training period, he tries to make sure that the apprentices are involved in the complete creation process of a piece of furniture. From on-site measurements, through pure production, to subsequent delivery and assembly, the junior employees are fully involved so that they can experience the entire development cycle.
The topic of inclusion is also very important to Stephan Ganz. A young man from his team has an intellectual disability, but this has no bearing on his place in the team. He is fully integrated and also an important cog in the entire development process of the work that is done in the workshop. He is a really positive part of the team, completing his tasks with great diligence and reliability.
Some of today's workforce have been trained in-house in previous years, proving how much value the company puts on promoting young talent.
Great vision even at a young age
Stephan Ganz himself can be described as an early starter. In 2009, when he was just 18 years old, he had just successfully completed his apprenticeship and already had the urge to stand on his own two feet. He started out as just a fitter. With a fully equipped truck, he drove to the customers' construction sites and completed the tasks assigned to him in full.
A couple of years later, in 2011, a neighboring property near his training company aroused his attention and curiosity. He bought it and wanted to start building work straightaway, but his friends and family put the brakes on, which he now describes as "completely right." He continued to work a further six years as a fitter until he had saved the necessary funds to be able to start the construction of his own four walls.
As a short intermediate step, before the construction of his own property, he rented a hall in Kürnach, where he had his first experiences as an established carpenter from 2015.
A milestone — The move to his own premises
In January 2018, the eagerly awaited construction of Stephan Ganz's own workshop and production hall began. A timber construction with a stud frame was chosen. In addition to thinking about sustainability, the focus was also on the feeling of well-being. "Wood is literally warm, whereas a hall made using a metal construction doesn't only feel cold, it is also visually cold," says Stephan Ganz. "Wood stores heat, which saves costs, especially in the transition months, because the heating doesn't have to be started immediately."
The renewable raw material from the forest not only looks friendly, but is also helpful when setting up or redesigning the workshop. Laying cables for power or compressed air is much easier. "Unlike a metal construction, it is easy to lay cables, drill holes or hang things from the ceiling, for example, such as the suction device," Ganz adds.
The move into the new premises was completed in the summer of 2018. To this day, Stephan Ganz is happy about the decisions made about the construction, the size of the chosen area and also the equipment and choice of the machines.
Early impressions influence decisions
During his own training, Stephan Ganz came into contact with machines from HOMAG. They made a very good impression, the experience was positive and it was then an obvious step to use machines from Schopfloch in his own company. The HOMAG sales representative from Denkendorf, Daniel Melder, provided very good advice. The machines were chosen so that they can easily compensate for the growth of the company in the next few years and an increase in the quantities of parts produced. This makes growth with HOMAG a sure thing!
With the HOMAG machines, Stephan Ganz can cover a large part of production. The machines are of course supplemented by classic joinery machines such as a circular saw, a dresser, a planer and a table router. To cut the workpieces, he purchased an HPP 130 (now SAWTEQ S-100) panel saw from the former HOMAG brand Holzma. It has been in regular use since 2015 and still delivers the most accurate cuts. Edge processing takes place on a KDF 440 C (now EDGETEQ S-300) from Brandt, also a former brand of HOMAG. Individual trimming work is done on the HOMAG CENTATEQ P-310 CNC processing center, which was not purchased until 2019.
Since the surfaces of the furniture and components produced are often refined, the final step when completing production follows is sanding and painting in the in-house clean room.
CNC processing is literally the center of attention
Just the acquisition of the CNC processing center and a wide-belt sanding machine has significantly increased Stephan Ganz's field of application. The CENTATEQ P-310 is not only the centerpiece in the workshop, but also in the production process. At first glance, it appears to be a bit too big for a company the size of the Ganz joinery, but here too, Stephan Ganz is thinking a few steps ahead and sees himself well set up for the future. The processing center is equipped with a five-axis head; this configuration alone allows almost anything that can be imagined. The high level of flexibility of trimming and drilling in the production enables custom batch size 1 concepts not only in furniture construction, but also in the production of staircases, and processing can be implemented on the CENTATEQ in a way that saves significantly more time than previously. The laborious process of creating templates for processing with the manual router is a thing of the past.
Before the HOMAG wide-belt sanding machine was purchased, processes such as intermediate sanding of painted panels or the calibration of solid table panels were difficult or even impossible. In addition, the sanding machine is equipped with a brush unit to highlight the structure of the wood when using solid parts. Right now, block-glued, solid oak is waiting to be transformed into a staircase.
HOMAG apps — The next step in digitalization
Since mid-November 2022, Stephan Ganz has been introducing digital products from HOMAG into his production. productionManager, the "digital job folder," brings transparency to the workshop. From now on, Ganz has access to all information about every job in real time — from the office through production and to the assembly area. The second tool of choice is intelliDivide Cutting, the optimization software for cutting on the saw. intelliDivide provides a choice of optimized cutting patterns in an instant. Depending on requirements, results can be based on minimizing waste or focus on the shortest machine running time or the simplest handling. The apps are the second step in the digitalization of the joinery. A planning software from IMOS with an integrated interface to the machines was introduced last year.
If something doesn't fit, it is printed to fit
The individual wishes of the customers are also reflected in individual in-house solutions within the scope of production. The Ganz joinery already consistently focuses on elements created using the 3D printing process as a matter of course. If the covers for sockets from the manufacturer's range don't fit, they are simply optimized, printed out in-house and created for individual use. Or are the door opening limiters on hinges for furniture doors not intended for the 90° opening? No problem.
They are re-designed and then simply printed out and installed in the furniture. The Ganz joinery is as pragmatic as its processes, easily dealing with all issues and focusing on solutions.
Modern heating thanks to the company's own chips
As early as 2018 when the company's own hall was built, the company had the foresight to take into account sustainability and resource conservation, topics that are particularly crucial right now. The chips extracted during production are immediately pressed into small briquettes and then burned in the in-house wood firing system and used for heating. The cycle is closed, the waste heat generated by the company in turn supplying the company with heat.
The roof areas of the hall constructed were also equipped with panels, which cover up to 35% of the electricity production required daily. This is a great contribution to protecting our environment.
At present, Stephan Ganz and his family are moving into their own premises on the upper floor of the workshop. He loves to combine his private and professional life and will therefore be able to benefit from the savings for electricity and heating in his home life in addition to his work life.
Ganz joinery
Stephan Ganz's business, which employs 10 people, is based in Rimpar, Germany, near Würzburg. Over an area of 960 m², of which 60 m² is allocated to office space, he creates many custom items for his customers, who are all within a radius of 100 km. Whether it's kitchens, staircases, doors, bathroom furniture, floors or even complete interior fittings, everything that can be produced from solid wood or wood panel material is in excellent hands at the Ganz joinery. They specialize in producing completely custom batch size 1 concepts for their customers.
More information