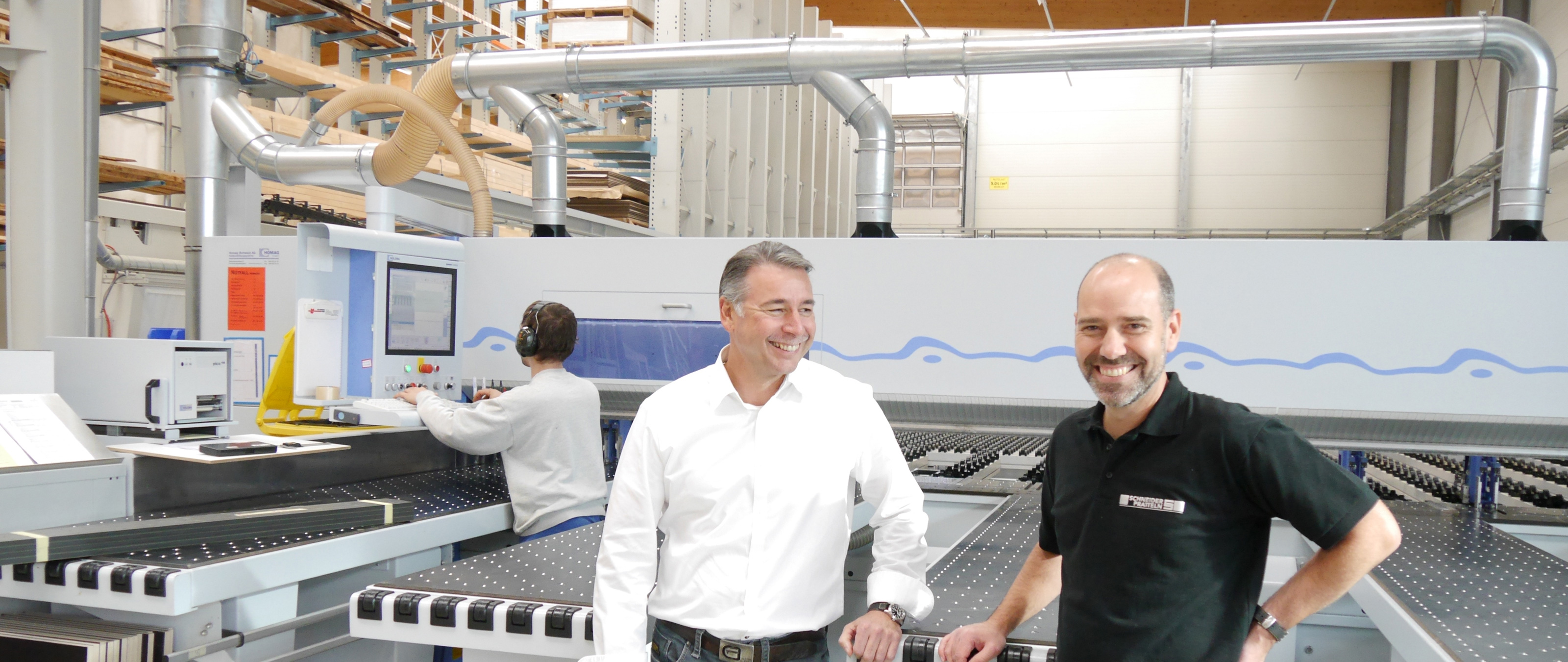
An article from the specialist magazine möbelfertigung, 07/ 2014, <link https: www.moebelfertigung.com issues emags _blank external-link-new-window article from the specialist magazine ausgabe>www.moebelfertigung.com
Not everyone is so lucky as to be able to plan a production facility on a greenfield site. Most companies grow on the spot and have to adapt their material flow in the production process to the available space. Efficiency is often one of the resulting casualties.
The Schneider Group, based in Pratteln, Switzerland, has experienced both situations. The company, managed today by the third generation of the family, was once bursting at the seams – until it relocated to a new building that more than anything else epitomizes "Swiss precision". The manufacturing facility: full of products from the Homag Group. The centerpiece of the production process: a large saw-storage combination from Holzma and Homag Automation.
But let's start at the beginning: Hugo Schneider, who founded the carpentry business in 1936, would be amazed today at the size and diversity of the company. One is almost tempted to ask: "What do you actually not make?" Because the original carpentry business has since developed into a whole group of companies. Under the umbrella of the Schneider Holding AG, you will find today not just the carpentry business but also other companies such as Systemtech and Coratec. These are all highly specialized firms – but they nevertheless have something in common: the carpenter's workshop. It is here, on the saw-storage combination, that all the panel materials are cut that then, among other things, go to the sister companies as component parts.
"In this way, we create synergies within the Group and benefit from each other," stresses Andreas Schneider, one of the sons of the company's founder and President of the Board of Directors of Schneider Holding AG. "This combination of different mainstays gives us entrepreneurial security," adds Karl Enderlin, Deputy Managing Director of Schreinerei Schneider. "Our employees are extremely flexible and are able to help out in one of the other areas if need be. Most of them enjoy this variety." Today, the Group employs some 120 people.
Schreinerei Schneider AG
The carpentry business is by no means merely a sub-supplier. It is specialized in, among other things, interior fittings for commercial and private customers. Most of these are based in northwest Switzerland, with some in Germany too. Customers include public authorities and renowned architects that gladly implement their ideas with Schreinerei Schneider. It therefore follows that batch size 1 production is part and parcel of day-to-day business.
At the time Hugo Schneider founded the business, window-making was part of the standard repertory of a carpenter. Today, it is a science in itself. The Schneiders, however, have always kept pace with developments, and that is why window-making is still part of their business activities. A great deal of solid wood is processed here to this day.
A perfect example for the ingenuity of Schreinerei Schneider is "dukta", an innovative, patented process by which cuts are made into one or both sides of wooden panel elements. This makes wood and timber-based materials very flexible and extremely sound absorbent, as well as giving them almost textile qualities.
Systemtech Schneider AG
Systemtech is specialized in fitting out railway carriages. A line of business that began back in the early years of the company because there happened to be a railway carriage manufacturer nearby who had a model made in the carpenter's workshop. The carriage manufacturer is no longer in existence; Systemtech, on the other hand, has successfully established itself in the market.
"We manufacture mainly wet-room and toilet systems," comments Enderlin, "and supply companies in Europe and worldwide." Customers include both large rail car manufacturers and direct customers such as government-owned or private rail operators. Anyone who thinks this is mass production business is mistaken. In Switzerland alone, there are more than 100 rail operators – and they all need new carriages every now and then.
Primarily, foamed plastic and metal elements are used. Nevertheless, wood plays a part too – as does the carpenter's workshop. At present, it is working on a very special order. "Systemtech is currently developing wet-room units for a hotel train for the Middle East," remarks Enderlin. "Railway lines there have gradients of up to 2. degrees. Furthermore, the carriages will be loaded onto a ferry. This means that the swell also has to be taken into consideration – this is crucial for the water supply. After all, we don't want a situation where a passenger standing under the shower doesn't get any more water or where suddenly while at sea everything is flooded." To be on the safe side, Schreinerei Schneider is building a moving wooden model of the train carriage to a scale of 1:1 for test purposes.
Another specialty is underfloor heating for railway carriages. This was developed originally for a customer in Norway four years ago. Here, the carriages stand in the open at temperatures reaching minus 40 degrees Celsius in winter and conventional heating systems take hours to raise the temperature inside to a comfortable level. The engineers at Systemtech therefore pressed various panel materials together and integrated a special heating system. They developed a highly sophisticated product that complies with the most stringent fire safety requirements and is extremely successful today.
Coratec AG
Coratec AG is another member of the Group. This company develops, produces and distributes composite elements. They consist of a very light core material and, depending on the requirements, different facing sheets made of aluminum, glass-fiber reinforced polyester or other materials. It is above all in the building industry and the vehicle construction industry that composites elements are in demand. They are used, for example, as side walls for containers or as floor panels for balconies. These composite panels can be enormous; it is not uncommon for them to be over six meters long.
A new home
These and other developments led to steady growth – which is why, in 2007, the company began to consider building a new production facility. However, success made planning a difficult task. This was because seven years ago Schneider had 40 employees. Then a phase of unprecedented growth set in, resulting in the number of employees increasing to 120 and turnover climbing to about 40 million Swiss francs (approximately 33 million euros). "New products such as the underfloor heating elements and the services offered by our newly established engineering department substantially increased turnover," reports Schneider. "It was only due to this growth that we were able to afford the new building and also new machines at the same time. One led to the other."
A real gem: the factory building
After an intensive planning phase, the building work went so much faster. Within a year, the factory building was finished, the machines were installed and everything was ready for production. Altogether, a space of 10,000 m³ was enclosed. Schneider: "To this day, we are very satisfied with the new factory building." It is 40 meters wide at the front and meters wide at the back, 10 meters long and 13 meters high. What is special about it is the fact that there are no columns, which means that every part of the factory building can be accessed by forklift trucks. "We planned in such a way as to allow sections of the building to be easily partitioned and let out if necessary. That did not happen. Today we need the entire space." About 80% of the electricity required is generated by the solar panel system on the roof.
The machinery
In the old building, Schneider was using a Brandt edge banding machine. There were no other Homag Group products. In the end, the machinery was no longer up to date, but the company wanted to wait until the forthcoming relocation had been completed before undertaking any large investments. "Despite this conscious restraint, the company decided to purchase a new CNC machine from us in 2008," observes Peter Niederer, Managing Director of Homag Schweiz. "If they had not done this, they would not have been able to continue producing." A model Venture Homag CNC machine was installed and its performance has been extremely convincing.
When relocation and complete renewal of the existing machinery was just round the corner, the Swiss company invited various suppliers for talks and also visited the Homag and Holzma factories. "It was a decisive factor for us that with the Homag Group we would be able to get everything from a single source," states Schneider. "It's an enormous advantage to have just one contact for all the machines. We were of course already familiar with the good quality and excellent service provided by the Group. Another important point was the fact that HOMAG Schweiz has its own team of service technicians and so can be on site fast, should it be necessary. This was and is a very significant aspect."
Determining factors for the first Homag CNC machine were processing size and speed. That is why a second one was installed in the new building right from the start. "Previously," Schneider continues, "we had four CNC machines in operation. Now we have just two – with much improved performance. I reckon that they are a good 40% faster than our old machines." A Bütfering sanding machine and a new Brandt edge banding machine were also installed.
The centerpiece: the new saw-storage combination
The cutting process is the linchpin for efficient production. This called for a modern saw-storage combination. In addition to the existing high bay storage area, which is still in use today, it was necessary to establish a horizontal storage system that would be capable of handling the wide range of materials. During the planning phase, the requirements in terms of panel size and weight increased. The cutting system was also to be able to cut the composite panels made by Coratec – and they come in sizes up to 6100 x 2200 mm. Peter Niederer explains: "Both saw and storage system had to be correspondingly large, leading to an increase in costs during the the quotation phase." Schneider smiles: "I was not at all happy about that." Then he adds: "But in the end it was worth it." The new saw-storage combination now meets every requirement and has already been amortized.
The machines from sister companies Holzma Plattenaufteiltechnik and Homag Automation (formerly Bargstedt) are perfectly compatible – a turnkey solution that impressed Schneider: "We decided on what was at that time a brand-new saw, the HPP 30 profiLine, with a cutting length of 600 mm in combination with a TLF 420 profiLine storage system."This saw boasts features that are still outstanding today, for example, the mineral casting machine base, which provides, among other things, a high level of precision and exceptionally smooth running.
When it came to configuring the saw, Schneider stuck with the principle: "Rather an option too many than laborious retrofits later." This is why the saw is also equipped with the "turbo grooving" option. "It is not very often that we use this option," says Enderlin, "but we are very glad to have it as it means we do not have to change to the CNC machine for grooving."
In order to be able to deal with even very hard materials such as HPL and compact panels, the saw works with a cut monitoring system. This stops the cutting process as soon as the saw blade no longer runs true. Furthermore, the saw is equipped with cutting gap closers to prevent narrow strips from falling into the cutting gap and blocking it. Other features include a minimum-quantity spray device, which is used when cutting plastic materials, a technology package for cutting laminate and trim stops to deal with overhanging facings. In order to ensure that the operator does not lose track of things due to the abundance of different materials, all the material-dependent parameters are set up in the saw control system and can be retrieved at the touch of a button.
Labeling of parts is completed fully automatically by a label printer located near the pressure beam. A feed-stacking table sees to it that the saw is not slowed down by the storage system; the store can stack panels for the saw here, while the saw is working at the front. The optimization software Cut Rite ensures efficient generation of cutting patterns.
The new TLF 420 profiLine storage system from Homag Automation is over 40 meters long and ideal for dealing with a wide variety of panels. Only offcuts that are larger than 200 x 80 cm are returned to the storage system. Smaller offcuts are disposed of automatically or managed manually.
The storage system has a high-end suction traverse and deposits the panels the right way round. This eliminates the need for an additional turning device or for large and heavy panels to be turned manually. The storage system is ideally equipped to deal with the great variety of materials and moves even porous or especially thick panels fully automatically. This has resulted in a fundamentally improved workflow. Above all, Enderlin appreciates the fact that he now always knows what he has got in stock and no longer has to spend days counting panels for stocktaking. "Now we can buy larger quantities and thus save a lot of money. The material needed the next day is automatically prepared overnight, thereby saving not just a lot of time but also money. In the old days, we used to be constantly on the go with the forklift truck. Nowadays, we rarely need to move material manually." The workforce is pleased about this, and another positive effect is that the amount of waste caused by transport damage has dropped substantially.
"We would make the same decision again."
Has the Schneider Group achieved its optimization targets in the production area? "We would make the same decision again," says Schneider, "but development is a never-ending process for us. We review workflows in the production process on a regular basis and recently also got a group of consultants in to do the same."
The company's success confirms that this is the right approach: only companies that are prepared to invest time and money in further development of their processes and products will be successful in the long term. Schneider puts it in a nutshell: "Just working is not enough. You must have new ideas too."
Images: Holzma/Schneider Holding AG
“Just working is not enough. You must have new ideas too.”Andreas Schneider, President of the Board of Directors of Schneider Holding AG