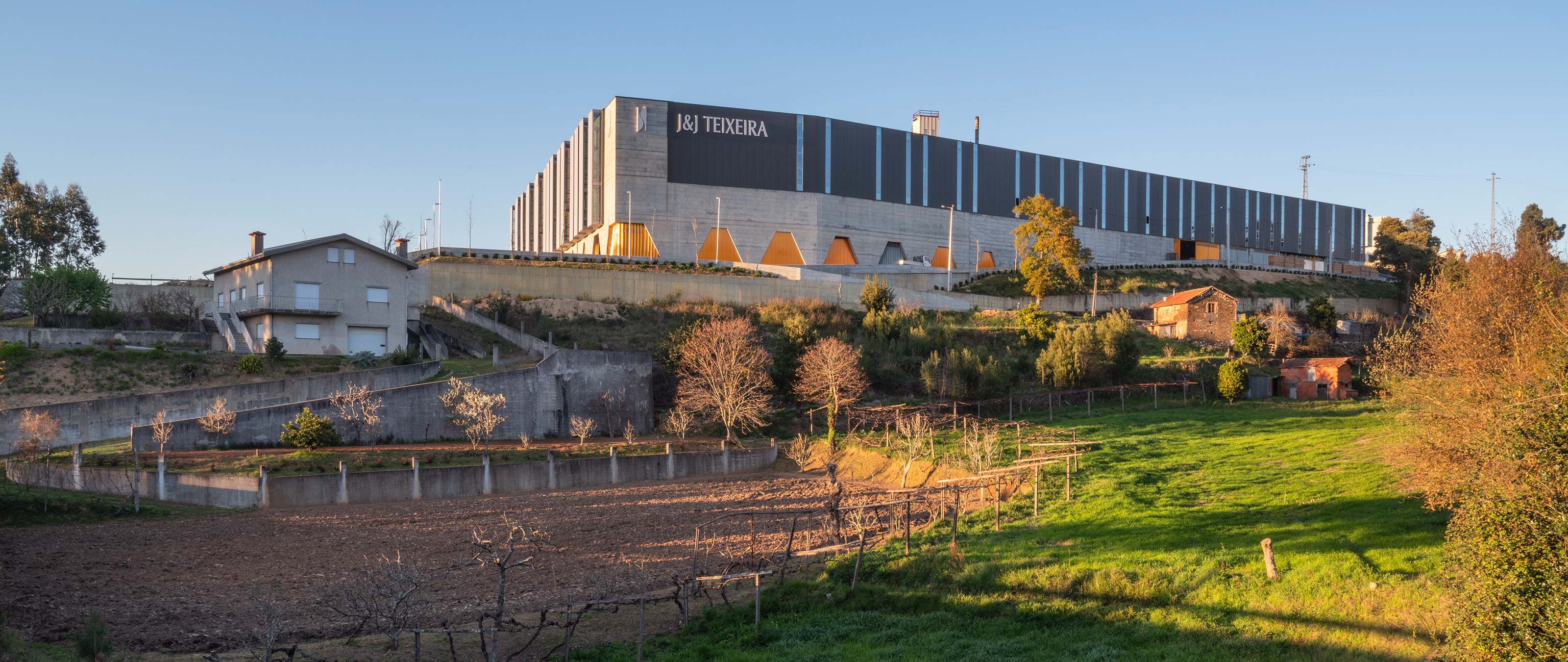
The Portuguese company J&J Teixeira not only produces furniture, but also furnishes entire buildings at the customer’s request – from window frames to television tables. The company combines pure craftsmanship with industrial series production. A fully automated production line from the HOMAG Group connects the two worlds and equips J&J Teixeira for the digital future.
Besides his full-time job as CEO, João Teixeira can often be found in his favorite place in the company: on the factory floor, which in total is as large as five football pitches. While there, the wiry man shakes hands with every employee and exchanges a few words with him or her. Not only is João Teixeira a polite man, he is also always on the lookout for new ideas to modernize production. “We can only be successful in the future if we are constantly improving,” says the Senior Manager, who founded the company in 1977. Since then, the family business (his children assist in key positions) situated on a gentle hill half an hour’s drive from Porto, has steadily grown.
Two and a half years ago, the Portuguese company took an important step towards the future. Teixeira launched a fully automated production line from the HOMAG Group, which saws, trims, drills and bands edges onto up to 4,000 single parts a day. The stations, which are spread out over 5,000 square meters, are networked with each other. Each workpiece can be identified using a barcode. A production management system programmed by the HOMAG Group controls the flow of the parts.
Indispensable technology
In light of the number of orders received, Teixeira can now no longer do without the plant. “Even if it only stops moving for a few moments, it soon gives us quite a headache,” says João’s son. Joaquim Teixeira is able to monitor each work step from his computer and respond immediately if any errors occur or maintenance is needed. All machines are prepared for tapio – the digital ecosystem of the HOMAG Group. In the future, tapio will enable users to download applications on smartphones and tablets that simplify maintenance, repair and production efficiency.
Teixeira builds parts for shelves, cabinets, kitchens or doors on the production line. Sometimes, these parts are sold separately. At other times, they are parts for a large project. After all, Teixeira furnishes entire buildings for his customers. His people build windows and doors for hotels, panel walls in office buildings or construct seating for concert halls and conference rooms. Always madeto-measure and according to the customer’s requirements. Around 150 out of a total of 350 employees work in the field.
The trained carpenter came up with his business idea when he founded the company at the age of 19. The customers enjoyed seeing him quickly sketch out his plans for furnishing their rooms. Architects soon recognized his talent. When he was 25 years old, he was given the opportunity to furnish large parts of the new Sheraton Hotel in Porto – from the cloakroom to the washbasins. It was his first major order and the start of a success story.
Teixeira’s own offices are now also showrooms that display the company’s aesthetic aspirations. The management area is separated from the factory floor by glass walls, giving employees a view of the production process. The atmosphere of each office is characterized by cold and warm color shades used in ever-changing ways. Smooth, polished, ribbed and matte surfaces alternate. The floors are covered with parquet in stick or fish bone patterns or with wide floorboards. Each room has different furniture – mostly made of wood.
Growth in Africa
Today, João’s first son, an architect, takes care of the designs. The diversity and creativity of the company are well known, not only in Portugal, but also overseas. More than 25 percent of the company’s turnover is generated in France and the UK. Some time ago, the company took a major leap and expanded into Angola and Mozambique. The common language certainly helped the business to establish in these countries. Now, companies as well as important authorities in other African countries rely on Teixeira. Thanks to his services, they no longer have to worry about importing materials or looking for suitable tradesmen in the country.
Many of Teixeira’s customers have unusual tastes. During a tour of the factory floor, Junior Manager Joaquim shows off a series of dark wooden doors with golden snorkels embedded into their surface. “These are for a customer in Ghana.” Another set of doors standing just a few meters away is also destined for Africa. They are edged with exceptional casket-style adornments.
The craftsmen at Teixeira have been making requests such as these a reality at their factory for many years. During the production process, the operators load the processed parts onto rail-guided trolleys and push them to the next station – just like the conveyor belt of a fully automated line would. There is just one difference: a manual process occasionally takes place at the stations that is often so unusual that it has to be carried out by hand, even today.
Can these processes, established over decades, be combined with a fully automated production line? This was the question on Teixeira’s mind when he visited a networked production line from the HOMAG Group for the first time during a technology tour in Austria in 2016. Despite some uncertainty, he was rapidly convinced: a plant like this needed to be part of his company soon. He asked the HOMAG Group for a quotation.
The planning process proved to be challenging. This was due to the fact that the predominantly manual production process in Teixeira’s old factory building was divided over three stories. Simply placing a fully automated line at ground level in a neighboring new building was out of the question. Firstly, because there was not enough room for this on the hilly site. Secondly, because the interface between manual processing and automatic production had to adjoin the top story in the existing building.
New construction is the best solution
The project team of the HOMAG Group thought long and hard about how to overcome this hurdle – and found an answer. “The best solution was to build a multi-story extension and to split the networked production line up over several levels,” says Achim Rauschenberger from HOMAG Sales. Naturally, Teixeira had also requested quotations from competitors. In the end, the HOMAG Group was awarded the contract. “They proved to be the most flexible and were able to implement our particular requirements in the best way,” says Teixeira.
Today, trucks deliver the raw chipboards to the first floor. A lift transports the tons of heavy material to the third floor to a digital HOMAG warehouse, where a robot-controlled overhead crane with vacuum grippers sorts them by thickness and color for cutting. A conveyor belt transports the trimmed and sawed parts to a decoupling buffer, where they then wait in its shelf-like compartments. This is also the location of the interface between the old and new production process. At specially designated stations, employees remove cut parts and transport them to the neighboring building complex on transverse sliding carriages. There, they are decorated, painted or furnished with individual grooves. The parts are then fed back to the production flow on a neighboring station.
The next station involves sizing and edge processing. Here, a wide variety of workpieces are sized before being banded cleanly and precisely with colorful edging strips. After this, the parts flow into a sorting buffer, which rearranges their order, an important step for the later stages of assembly and dispatch. “The buffer also serves as a transport lift,” explains Teixeira. It extends over two stories and can hold more than 4,000 parts. The central control system always knows where each one of them is. One story down, the parts are drilled and then placed back onto the conveyor belt by robots, where they move onto the assembly line and then to packaging.
Currently, assembly still has to be completed by hand. However, Teixeira has concrete plans to automate this task in the near future. The backlog of orders is growing and he needs his employees elsewhere. “We are always looking for new ways to expand the line and to increase our productivity,” says Teixeira, shortly before saying goodbye and continuing his tour of the factory – on the lookout for new ideas.
“We can only be successful in the future if we are constantly improving.”João Teixeira, CEO J&J Teixeira
More about J&J Teixeira
The Portuguese company J&J Teixeira not only produces furniture, but also furnishes entire buildings at the customer’s request – from window frames to television tables. The company combines pure craftsmanship with industrial series production.
www.jjteixeira.pt