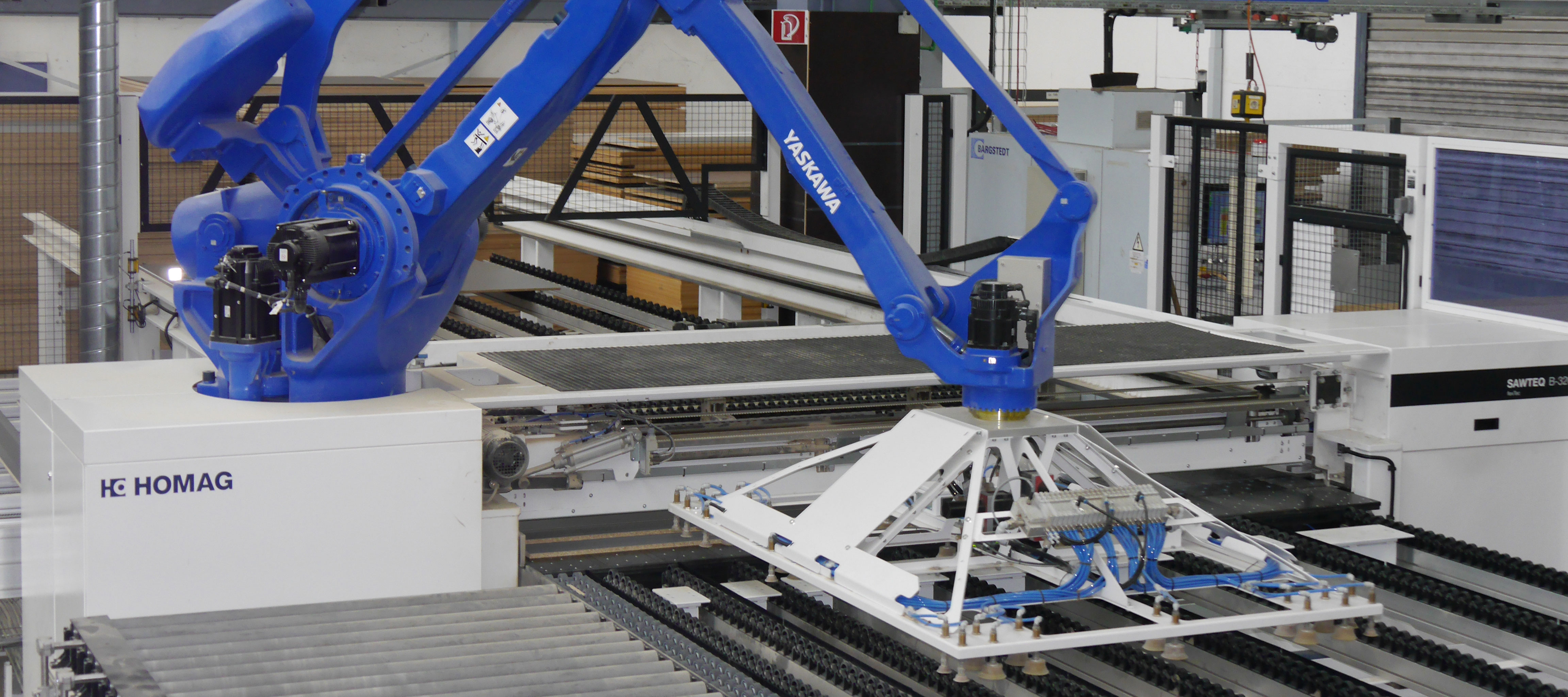
Speed and flexibility are very important for those in charge at Duravit. That's why the bathroom furniture manufacturer purchased two identical saw systems with robotic feed from Homag Plattenaufteiltechnik. The saw systems are supplied with unprocessed materials from automatic panel storage systems. By using industrial robots, Duravit achieves almost 100 percent availability. HK visited the company in Schenkenzell.
"We have around 87,000 current parts as well as 20,000 phased-out parts that we must be able to produce immediately," says Ulrich Weber, Dipl. Ing. (FH) and plant manager of the Duravit AG furniture factory in Schenkenzell in the Black Forest, describing his work and tasks. "However, we don't have any storage space for furniture parts—each part in production is part of a commissioned order." It therefore makes no difference how big the part is. There are two storage systems in the automatic manufacturing process, but these are the layer and sorting buffers. Together, they ensure that in the formatting machine, there are as few changeovers as possible, and the cutting function can process the cutting patterns optimally. In total, 20 criteria have been developed and defined in the production control system at Duravit to achieve the greatest possible efficiency.
Ulrich Weber joined the bathroom furniture manufacturer in 1993 and has contributed substantially to the development of the factory, which, until 1992, was a cloth factory. The sanitary ware manufacturer wanted to increase its production depth and also include bathroom furniture and washbasin cabinets in its portfolio. As a young plant manager, Weber had the will to achieve an optimum production flow from the very start. And with his team, he has done just that.
Anyone visiting the Duravit furniture factory in Schenkenzell today will rub their eyes in amazement, thinking they are visiting a production plant in the automotive industry. The entire production is organized fully automatically and protected by two-meter high protective fences. Footbridges prevent visitors or workers from disrupting the production flow. "With the high level of automation, we have also achieved an increase in quality because there is almost no damage to the components anymore," explains Ulrich Weber. That starts with the cutting. There are two identical saw systems, each consisting of one "Sawteq B-320 flexTec" with robot handling. Both systems are connected to the entire, industrially organized production via roller conveyors and conveyor belts. Both "robot saws" are supplied with panel materials from two storage systems, which are computer controlled and organized randomly. These are storage systems that, under the new Homag naming convention, correspond to the "Storeteq S-500."
The second storage system is located in a neighboring hall and has a storage capacity one third greater. As they are needed, the unprocessed panels are transported to warehouse 1 by forklift truck and then taken over there by the computer control system.
The storage system also takes over the storage and sorting as well as the removal from storage at the saws, which are designed as dividing cells for the individual cutting of individual panels and the order-related production. The production control bundles the customer orders according to material type in order to generate as little waste as possible. Once the relevant cutting patterns have been processed, the parts that do not have to be edged go directly to destacking. Components that are to receive an edge are buffered in a "Sorteq H-600" layer storage, which acts as a decoupling buffer, and are fed to the single-sided "Edgeteq S-800" edge processing machine as required via intermediate transport. This means that parts of different sizes can be run one after the other, depending on the commission.
The "Loopteq C-500" edge circulation is designed as an O-line, in which the components are fully edged in up to three throughfeeds. The components then go into a "TLB 210" 4-bin sorter or directly for destacking. The stack station with robotic stacking ensures that the components of a sorting batch are removed from storage in the specified order. Depending on the functionality, the components are also fed to processing centers, which perform component-specific routing, drilling and sawing work. Some of the workpieces also go to painting, where customer-specific paints are applied. This is where the benefits of commission-based production come to the fore.
The robots contribute significantly to the success of the entire production line as they move the panels with vacuum technology that gently handles the materials. Their precise movements also ensure maximum quality. According to the company's own information, production stoppages are virtually ruled out thanks to the tried-and-tested industrial robot, allowing almost 100 percent availability. What's more, the error rate is extremely low.
The label printer with the integrated control scanner labels all parts fully automatically, whereby each saw system has its own printer that attaches the barcode label to the cut part just before the part exits the system. The labels contain all the information required for subsequent processing steps.
With an output of up to 1500 parts per machine per shift, the unit costs in batch size 1 production are thus significantly reduced. What visitors don't see straight away when considering the production sequences is the performance of the computer, which works away quietly and reliably in the black box. It is the Homag system, which is networked with the "Controller MES" control system, that enables the user to achieve their goals. To do this, the "Controller MES" takes over the customer and production orders from the Duravit planning system and relays the data to the control systems of the individual processing machines.
"What sounds so easy in the sales discussion then looks significantly different in practice," says Ulrich Weber, recounting his experiences. "I would advise anyone wanting to buy such a system to think about the IT involved in implementing something like that." For Ulrich Weber, the investments in the two "robot saws" and the automatic formatting machine cannot be covered by a simple amortization calculation. "That's because we didn't just buy machines, we changed our system and set ourselves up for the future," says Weber. Of course, the plant manager himself knows what value having one less employee represents in the amortization calculation. But how can you translate shorter delivery times, higher quality, flexibility and high plant availability into figures?
Ulrich Weber does not answer this but has already discovered a new field of activity. He wants to reduce the waste produced on his "robot saws." "Every percentage point reduction saves us EUR 50,000" he says astutely.
“With the high level of automation, we have also achieved an increase in quality because there is almost no damage to the components anymore”Ulrich Weber, plant manager of the Duravit AG in Schenkenzell